
Textile manufacturing is the backbone of the global fashion industry, covering the transformation of fibers into fabrics and fabrics into finished products such as clothing, upholstery, and industrial materials. This dynamic sector had a global market size valued at $1,837.27 billion in 2023 and is projected to grow at a CAGR of 7.4% from 2024 to 2030, fueled by rising demand for sustainable and technologically advanced textiles.
Why does it matter? Beyond clothing, textiles play a crucial role in sectors like healthcare, agriculture, and construction. However, challenges like environmental impact and resource scarcity are reshaping how the industry operates. From cotton spinning in traditional mills to modern systems powered by AI, textile manufacturing remains at the forefront of industrial innovation.
With advanced trend forecasting solutions like Heuritech, brands can anticipate shifts in material demand, optimize production planning, and reduce waste—ensuring a more sustainable and data-driven approach to textile manufacturing.
The Basics of Textile Manufacturing
Textile manufacturing is the process of transforming raw fibers into finished materials like fabrics and clothing. It begins with fiber sourcing, which can be natural (cotton, wool, silk) or synthetic (polyester, nylon). While cotton remains the most widely used natural fiber, synthetic fibers dominate modern production due to their durability and cost efficiency. However, their widespread use comes with significant environmental concerns: synthetic textiles are derived from petrochemicals and contribute to microplastic pollution, with textiles accounting for approximately 9% of annual microplastic losses to the ocean. The production and washing of synthetic fabrics release plastic particles that persist in ecosystems, highlighting one of the fashion industry’s most pressing sustainability challenges.
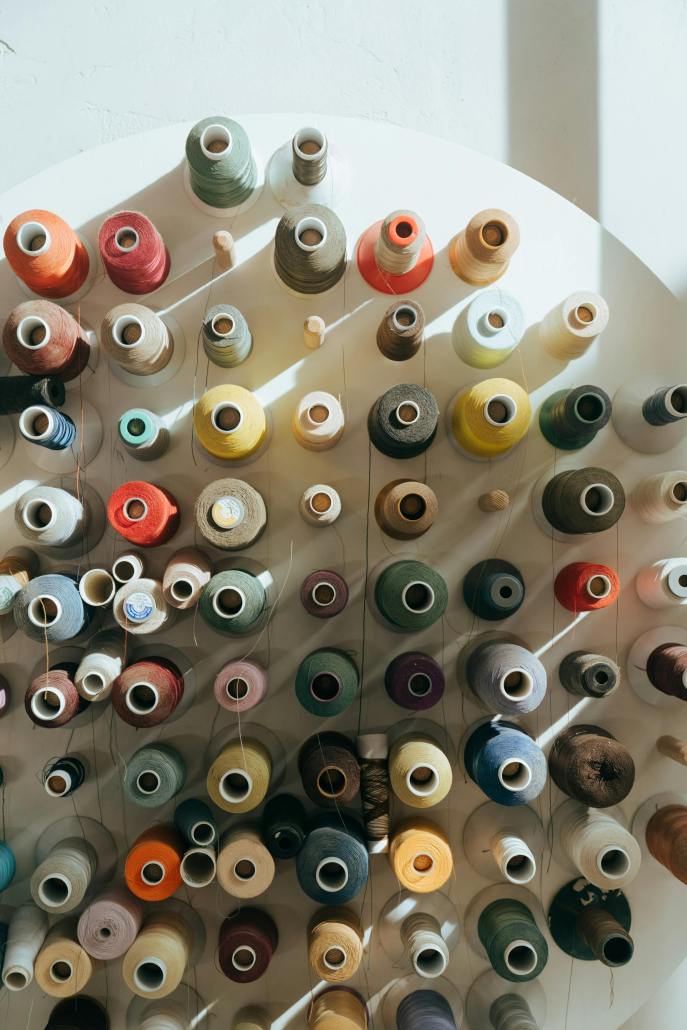
The process includes:
Spinning: Converting fibers into yarn by twisting them for strength.
Weaving or knitting: Turning yarn into fabric through interlacing or looping techniques.
Dyeing and finishing: Adding color and texture to fabrics, as well as treatments like water resistance or anti-wrinkle properties.
Traditionally, much of this work was done manually or on basic looms, but today, automation and advanced machinery are the norm. This shift ensures greater efficiency, quality control, and the ability to produce fabrics at scale.
Whether it’s a soft wool sweater or a synthetic outdoor jacket, the fundamentals of textile manufacturing remain rooted in turning fibers into materials that serve functional and aesthetic purposes.
Challenges Facing the Textile Industry
Textile manufacturing is evolving under immense pressure to address sustainability, supply chain fragility, and workforce transitions. These challenges are interconnected, demanding a holistic response from the industry.
Sustainability Pressures
Sustainability in the textile industry is no longer optional—it’s a necessity. Textile production is among the most resource-intensive industries, with severe environmental impacts at every stage of the supply chain.
One of the most pressing concerns is water consumption. Producing a single cotton shirt requires approximately 2,700 liters of water, enough to meet an individual’s drinking needs for over two years. The textile sector was the third-largest contributor to water degradation and land use in the EU in 2020, consuming an average of nine cubic meters of water per person annually. Additionally, textile dyeing is responsible for 20% of global industrial water pollution, with dye effluents contaminating rivers and oceans, increasing chemical oxygen demand, and threatening aquatic biodiversity.
Beyond water pollution, textile waste and microplastics represent a growing environmental crisis. Every year, the industry generates vast amounts of waste—on average, Europeans discard 11 kg of textiles per person annually, with 87% ending up in landfills or incinerators. Only 1% of used clothing is recycled into new garments, as existing recycling technologies struggle to break down complex fiber blends. Furthermore, synthetic textiles like polyester release microplastics into waterways. A single laundry load of polyester garments can shed 700,000 microplastic fibers, which accumulate in marine ecosystems and the food chain. More than half a million tonnes of microplastics from textiles settle in the ocean floor annually.
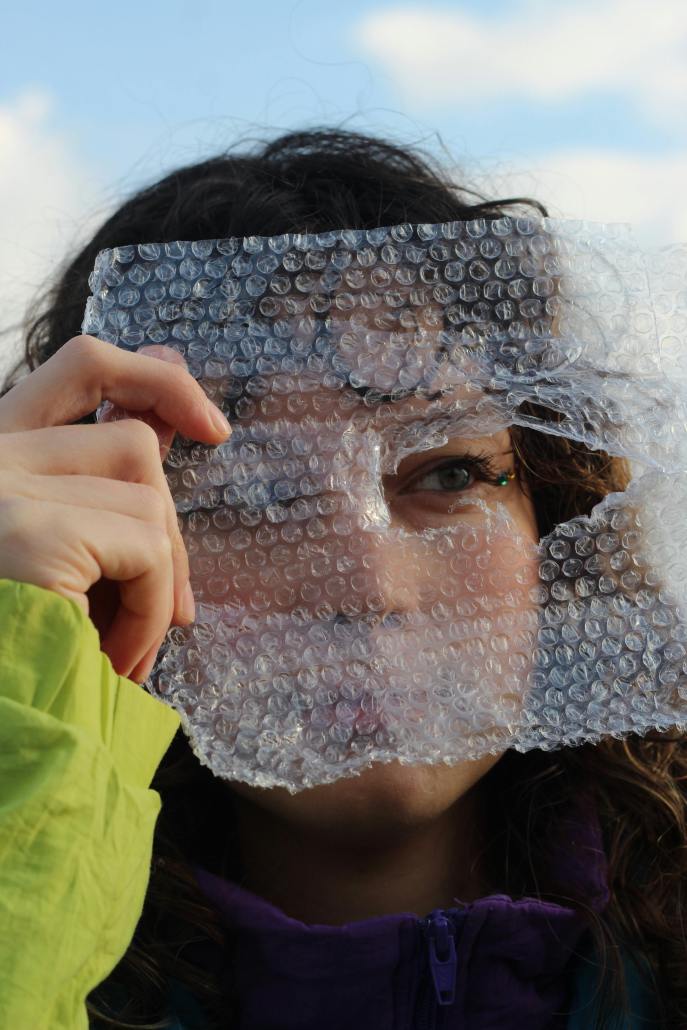
Faced with these challenges, manufacturers are pivoting toward more sustainable solutions, such as:
- Recycled fibers, reducing reliance on virgin raw materials and limiting waste. Some brands are incorporating post-consumer textile waste or using ocean plastic to create new fabrics.
- Waterless dyeing technologies, such as CO₂-based dyeing systems, which eliminate the need for water and significantly reduce chemical runoff.
- Circular production models, where waste fabrics are reintegrated into new products, reducing landfill waste and extending product lifecycles.
- Eco-friendly dyeing alternatives, including biodegradable and plant-based dyes, which minimize the harmful effects of synthetic dyes on human health and aquatic life.
Governments and regulatory bodies are also stepping in to address the industry’s footprint. The EU Strategy for Sustainable and Circular Textiles, introduced in 2022, mandates ecodesign requirements, digital product passports, and extended producer responsibility (EPR) schemes, holding brands accountable for the entire lifecycle of their products. By 2025, EU countries will be required to collect textiles separately for reuse and recycling.
While progress is being made, the road to sustainability requires continued innovation and systemic change. Shifting towards circularity, embracing slow fashion principles, and adopting cutting-edge technologies will be critical to mitigating fashion’s environmental toll while aligning with growing consumer demand for responsible production.
Supply Chain Complexities
Global supply chains in the textile industry have become increasingly fragile, with multiple risk factors disrupting operations at various stages—from raw material sourcing to production and logistics.
Raw Material Shortages & Climate Change
Extreme weather events and climate change are significantly impacting the availability of raw materials. Droughts, floods, and rising temperatures are affecting cotton-growing regions, leading to lower yields and reduced quality. In recent years, droughts in major cotton-producing countries such as India, the U.S., and China have constrained supply, forcing manufacturers to seek alternative fiber sources. Additionally, heatwaves and erratic rainfall patterns are making it harder for farmers to plan their production cycles, increasing unpredictability in the market.
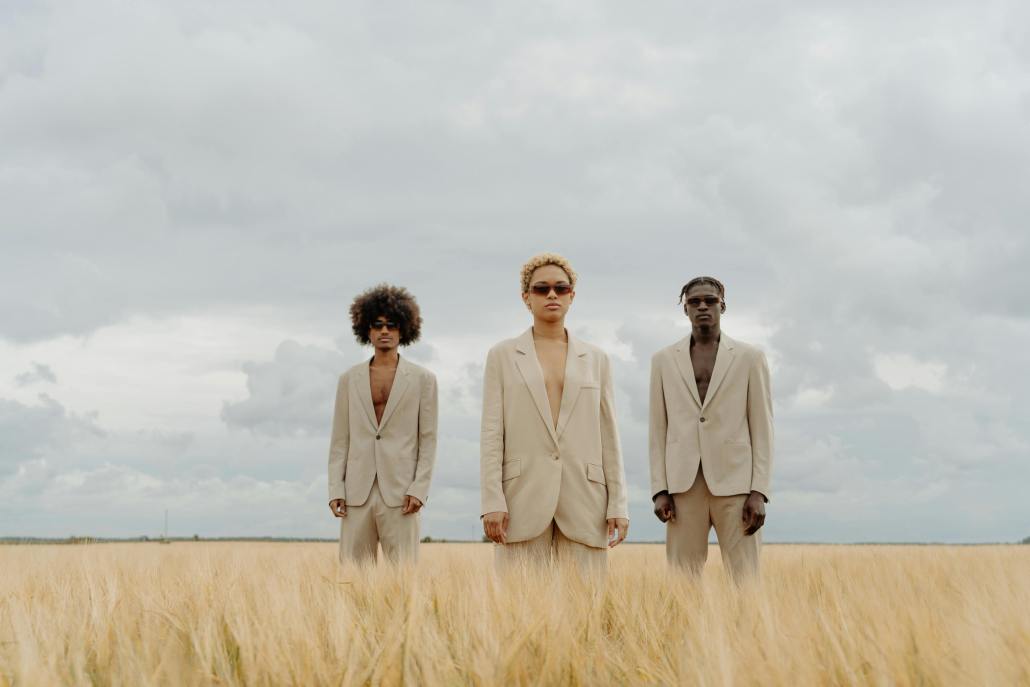
Price Volatility & Market Instability
The volatility of commodity prices is another major challenge. In 2022, cotton prices fluctuated drastically, peaking at 135.25 cents per pound on August 30 before dropping to a low of 72.26 cents per pound on June 28, 2023. By the end of the year, prices had settled at 101.62 cents per pound—a 23% decrease from their highest point. These fluctuations are driven by supply chain disruptions, changing consumer demand, and external shocks such as inflation and currency depreciation. Raw material instability directly impacts production costs, leading to pricing pressures for brands and retailers.
The Push for Diversification & Resilient Supply Chains
To counteract these challenges, companies are adopting diversified supply chain strategies aimed at increasing flexibility and reducing risk exposure. Some key approaches include:
- Nearshoring & Regionalized Production: Brands are relocating manufacturing closer to consumer markets to shorten lead times and reduce transportation dependencies. This trend is particularly noticeable in Europe (with increased production in Turkey and Portugal) and North America (with Mexico and Central America emerging as key production hubs).
- Supplier Diversification: Rather than relying on a single supplier or region, businesses are expanding their sourcing networks across multiple countries to ensure continuity even in the face of localized disruptions.
- Digitization & Supply Chain Transparency: Companies are investing in AI-driven demand forecasting, blockchain-based traceability, and real-time tracking systems to enhance supply chain visibility and predict potential disruptions before they escalate.
As the textile industry continues to navigate these complex challenges, building resilient, adaptive, and sustainable supply chains will be crucial for long-term success.
Workforce and Automation
Automation has reshaped textile production by streamlining tasks like spinning and weaving, improving efficiency and reducing costs. However, this shift threatens millions of jobs in labor-dependent regions such as Southeast Asia. To bridge the gap, manufacturers are investing in upskilling programs, training workers in digital tools and machine operation to transition into higher-value roles. At the same time, hybrid workflows are emerging, where automation handles repetitive tasks while human expertise ensures quality control and craftsmanship. Balancing automation with workforce adaptability is key to a sustainable transition
Balancing Quality and Scale
As consumers demand higher-quality, customized products, manufacturers face new challenges:
- Ensuring uniform fabric quality across large batches.
- Meeting niche customization needs without disrupting mass production.
AI-powered tools are emerging as a solution, offering predictive maintenance for machinery and enabling agile production systems that can adapt to varying demands.
Key Trends in Textile Manufacturing for 2025
The textile manufacturing landscape is evolving rapidly, driven by changing consumer demands, technological advancements, and global market dynamics. Here are the key trends shaping the industry in 2025, based on our predictive insights at Heuritech.
1. Sustainable Textiles Take Center Stage
Sustainability is not just a buzzword—it’s a necessity. Consumers and regulators alike demand greener practices, prompting manufacturers to adopt:
- Recycled materials: Polyester made from post-consumer plastics and textiles.
- Organic fibers: Cotton and wool grown with minimal chemical inputs.
- Waterless processes: Technologies reducing dyeing water use by up to 90%, such as ECOHUES™, which replaces water with a recyclable non-aqueous solvent, cutting water usage by 95%, and DyeCoo, which uses pressurized CO₂ instead of water, eliminating wastewater discharge entirely.
By 2030, the global sustainable fashion market is projected to grow from USD 15.01 billion in 2025 to USD 47.48 billion, reflecting a CAGR of 15.48%. This rapid expansion highlights the increasing market share of sustainable fashion brands as consumer demand for eco-friendly alternatives rises
2. Localization of Production
The shift towards localized production in the fashion industry is more nuanced than a straightforward move away from global supply chains. While nearshoring and regionalization are gaining traction—allowing brands to reduce shipping costs and supply chain bottlenecks—this is not a universal trend. Many companies still rely on global sourcing, with China alone accounting for 36.5% of all imported clothing items in the U.S..
Geopolitical factors are also shaping sourcing strategies. Brands are increasingly selecting suppliers from geopolitically aligned regions, leading to a shortened sourcing footprint in countries like China, Germany, the UK, and the US. However, full localization remains challenging due to the need for specialized skills, higher local production costs, and raw material availability.
As a result, many fashion brands adopt hybrid supply chain strategies, blending global and local sourcing to balance cost, speed, and resilience. This approach allows them to adapt to disruptions while maintaining flexibility in production and distribution.
3. Demand for Performance Fabrics
Functionality is no longer optional in textiles. The growing athleisure and outdoor wear markets are driving demand for:
- Moisture-wicking and odor-resistant fabrics.
- Stretchable, breathable fabrics ideal for active lifestyles.
- Weatherproof textiles, including UV-blocking and waterproof materials.
According to Heuritech data, opaque rainproof fabric will grow 15% during the Winter 2025 season in Europe, and 12% in Brazil:
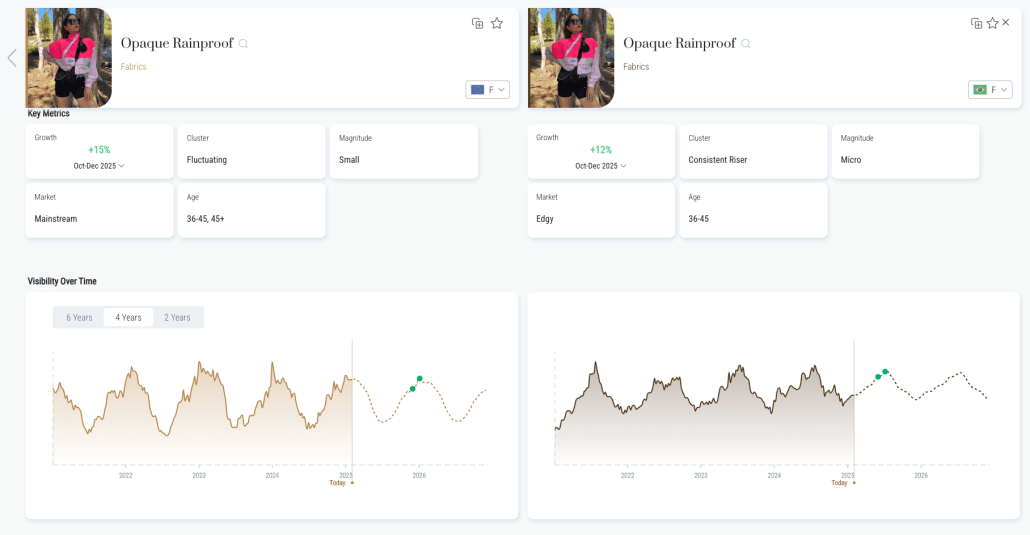
Image: Data from Heuritech Market Insights
By 2025, the performance fabrics market is projected to grow at a CAGR of 5.02%, reaching USD 84.60 billion, with an expected market size of USD 108.02 billion by 2030. This steady growth reflects increasing demand across industries such as sportswear, healthcare, and industrial applications, making it a key segment for innovation and investment.
4. Customization and On-Demand Manufacturing
Modern consumers seek individuality, and brands are responding with on-demand production:
- Digital printing enables high-quality, customizable designs at scale.
- On-demand systems eliminate overproduction, reducing inventory by up to 40%.
- Small-batch, personalized collections are becoming mainstream, especially in premium and luxury markets.
5. The Rise of Circular Fashion
The shift towards circularity is redefining how textiles are produced and consumed:
- Fabric recycling technologies can convert used garments into new fibers.
- Take-back programs incentivize consumers to return old clothing for reprocessing.
- Brands incorporating circular practices are expected to see higher consumer loyalty, with surveys showing 60% of shoppers prioritize sustainable options.
6. Emerging Markets in Textile Manufacturing
New regions are gaining prominence in textile production:
- Africa: Nations like Ethiopia and Kenya are becoming low-cost manufacturing hubs with an emphasis on ethical production.
- South America: Countries such as Brazil are focusing on bio-based textiles derived from local resources.
Emerging markets are diversifying global production networks and introducing innovative, locally sourced materials.
7. Digitization of the Textile Industry
The textile industry is undergoing a major digital transformation, driven by Industry 4.0 technologies. Smart factories are leveraging IoT for real-time monitoring, predictive maintenance, and efficiency gains, while AI-driven decision-making helps optimize inventory and production planning. Additionally, blockchain is enhancing transparency in sourcing and sustainability verification, and cloud-based ERP solutions are providing scalable and cost-effective management tools. While adoption rates vary, trends indicate significant global growth—for instance, 29% of textile companies in Brazil have already implemented Industry 4.0 solutions, a number expected to rise.
This digital transformation is essential for streamlining operations and maintaining competitiveness in an increasingly tech-driven market.
Heuritech’s Insights: Empowering Brands for 2025
At Heuritech, our AI-powered solutions offer precise, data-driven forecasts, enabling brands to align with these emerging trends. From predicting material preferences to identifying regional demands, our technology ensures manufacturers are ready to innovate and thrive in the evolving textile landscape.
If you want to see our technology in action, we invite you to explore our interactive demo. Experience firsthand how our AI-driven insights can help your brand stay ahead of trends, optimize production, and make informed decisions with confidence.
Book a demo and discover the future of textile forecasting.